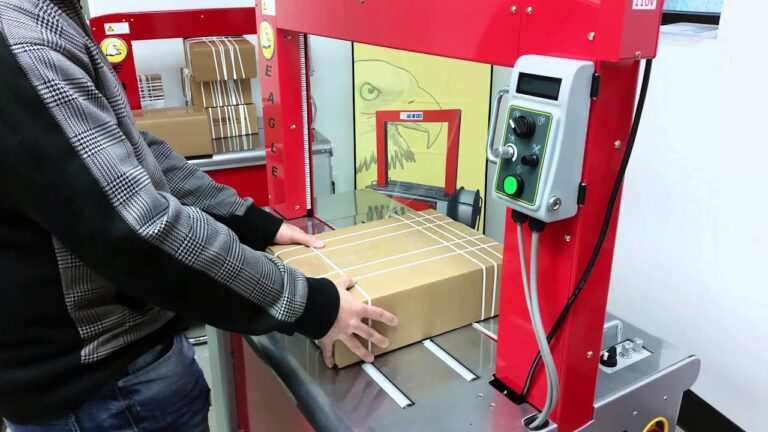
Buyer’s Guide to Strapping Systems: Choosing the Right Fit for Your Operation
July 4, 2025
0 Comments
Strapping systems are essential tools for securing shipments, bundling products, and improving the efficiency of your packaging line. Whether you’re a small business shipping a few boxes a day or a high-volume operation managing hundreds of cases per hour, choosing the right strapping equipment can save time, reduce labor costs, and ensure your products are well-protected in transit. This buyer’s guide walks you through three common types of strapping systems—hand-held machines, tabletop machines, and arch strap machines—and how to choose the best fit for your needs based on volume, case size, and budget.
Hand-Held Friction Weld Strapping Tools: Best for Low-Volume Operations
If your team currently straps boxes manually with buckles or metal seals, a hand-held friction weld strapping tool can be a game changer. These battery-powered tools tension, weld, and cut strapping in a single motion—eliminating the need for clips and significantly speeding up the process. They’re ideal for operations that are growing but not yet ready to invest in fully automated solutions.
These tools are mobile, easy to operate, and work with a variety of plastic strapping widths, making them great for strapping pallets, irregularly shaped packages, or bundles that vary in size. While the upfront cost (typically $1,500–$3,000) is higher than manual tools, the time savings and improved consistency quickly justify the investment. However, they’re still reliant on manual labor, so they’re best suited for businesses with lower daily volumes or operations requiring mobility in strapping.
Tabletop Strapping Machines: Ideal for Medium-Volume Workflows
When your operation reaches a consistent medium volume—say, dozens to a few hundred packages per day—a tabletop or benchtop strapping machine offers an excellent balance of speed, efficiency, and affordability. These semi-automatic machines require an operator to place the box on the table and initiate the strap cycle, but the machine handles the feeding, tensioning, sealing, and cutting.
Benchtop strappers are compact, typically costing between $1,000 and $4,000, and are perfect for operations with uniform case sizes and a centralized packaging station. They’re an ideal step up from manual or hand-held tools for businesses looking to reduce labor fatigue andincrease throughput without committing to a large capital expense. However, they may not be the best solution for very large or irregularly shaped cases.
Arch Strapping Machines: Best for High-Volume and Large Case Applications
For high-volume packaging lines, especially in warehousing, e-commerce, or manufacturing, arch strapping machines deliver maximum speed and automation. These fully automatic machines can strap hundreds of packages per hour with minimal operator involvement. Packages simply move through the arch—either manually or via a conveyor—and the machine automatically straps each item in seconds.
Arch machines are highly customizable, with different arch sizes to accommodate everything from small boxes to large shipping cases. They are best suited for operations with standardized case sizes, high throughput, and space for a dedicated line. While these systems come with a higher upfront cost (typically $7,000–$20,000+), they offer exceptional labor savings and throughput gains—often paying for themselves in a matter of months.
Final Thoughts
Choosing the right strapping system depends on your packaging volume, case sizes, and budget. Hand-held friction weld tools are perfect for small but growing operations; tabletop machines offer a balance of speed and flexibility for medium-volume workflows; and arch strapping machines are the gold standard for high-volume facilities. With the right solution in place, you’ll improve efficiency, reduce labor strain, and ensure every package leaves your facility secure and ready for transit.